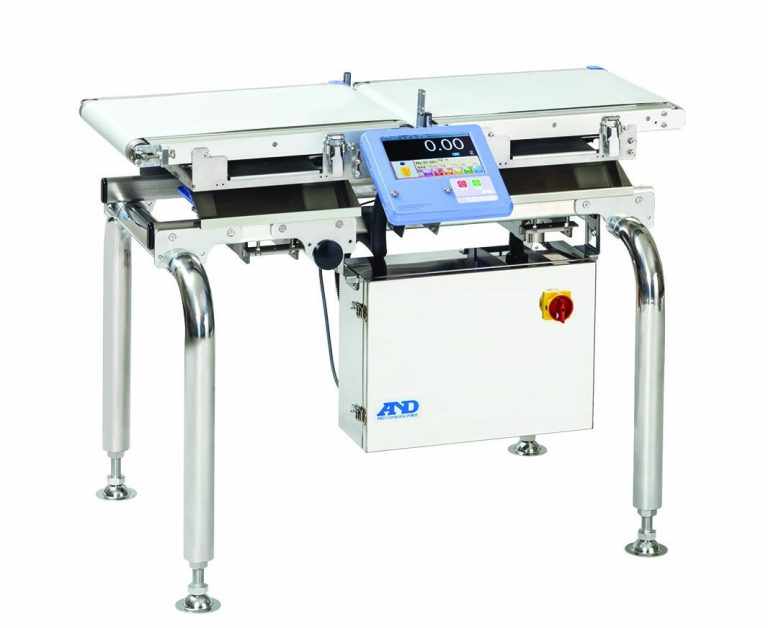
Industrial checkweighing plays a crucial role in various industries, from food production to pharmaceuticals and manufacturing. It ensures that products meet specified weight requirements, helping to maintain quality control, reduce waste, and comply with regulatory standards. However, despite its importance, checkweighing systems can present a range of challenges that can impact efficiency and accuracy.
1. Inaccurate Weight Measurements
Challenge:
One of the most significant issues in checkweighing is inaccurate weight measurements. Inaccuracies can arise due to various factors, such as environmental conditions, improper calibration, mechanical wear and tear, and operator errors.
Solution:
Regular Calibration: Frequent calibration using certified test weights ensures accuracy and consistency in weight measurements.
Environmental Control: Install checkweighers in areas with stable temperatures and minimal air currents to reduce fluctuations in weight readings.
Proper Maintenance: Regularly inspect and maintain weighing components to prevent mechanical failures.
Operator Training: Educate staff on proper checkweighing procedures to minimize human error.
2. Product Flow Disruptions
Challenge:
Disruptions in product flow can lead to downtime, bottlenecks, and inefficiencies in the production line. These disruptions may be caused by irregular product spacing, improper conveyor belt speeds, or mechanical failures.
Solution:
Automated Product Spacing: Use automatic product spacing systems to ensure consistent gaps between items.
Optimize Conveyor Speed: Adjust conveyor speeds to align with production needs while maintaining accuracy.
Routine Equipment Inspection: Regularly check conveyor belts, rollers, and guides for wear and tear to prevent unexpected failures.
3. High Rejection Rates
Challenge:
A high number of rejected products can lead to increased waste, financial losses, and inefficiencies in production. False rejections may occur due to minor weight variations, inconsistent settings, or misaligned rejection mechanisms.
Solution:
Fine-Tune Tolerance Levels: Set appropriate weight tolerance levels based on industry standards and product specifications.
Check for Mechanical Misalignments: Ensure that rejection systems (such as air jets or pushers) are properly aligned to prevent unnecessary discards.
Implement Data Analytics: Use checkweigher data to identify patterns and trends in rejected products, enabling proactive adjustments.
4. Regulatory Compliance Issues
Challenge:
Different industries have strict weight compliance regulations that manufacturers must adhere to. Failing to meet regulatory requirements can lead to legal issues, fines, and reputational damage.
Solution:
Stay Updated on Regulations: Regularly review industry-specific regulations and ensure that your checkweighing system complies with them.
Automate Compliance Checks: Implement software that monitors compliance and generates reports for auditing purposes.
Conduct Internal Audits: Schedule periodic internal audits to verify adherence to regulatory standards.
5. Integration with Other Systems
Challenge:
Integrating checkweighers with other automated systems, such as packaging lines, ERP software, and quality control databases, can be complex. Poor integration can lead to data silos and inefficiencies.
Solution:
Use Compatible Software: Select checkweighing systems that support standard communication protocols such as Ethernet, Modbus, or OPC-UA.
Work with IT Experts: Collaborate with IT specialists to ensure seamless data transfer between checkweighers and enterprise systems.
Test Integration Before Full Implementation: Conduct pilot tests to identify potential integration issues and resolve them before full-scale deployment.
6. Wear and Tear on Equipment
Challenge:
Industrial checkweighers operate in demanding environments, leading to wear and tear on components over time. This can result in frequent breakdowns and costly repairs.
Solution:
Preventive Maintenance: Establish a routine maintenance schedule to inspect and replace worn-out parts before they fail.
Use Durable Materials: Invest in high-quality checkweighing equipment designed for industrial use.
Monitor Equipment Performance: Utilize IoT-enabled sensors to track wear and tear, enabling predictive maintenance.
7. Handling a Wide Range of Product Types
Challenge:
Manufacturers dealing with diverse product lines may face difficulties in configuring checkweighers to handle different shapes, sizes, and weights efficiently.
Solution:
Use Adaptive Weighing Technology: Invest in checkweighers with dynamic adjustment capabilities to accommodate various product types.
Customize Checkweighing Settings: Configure settings based on product characteristics to ensure accurate measurements.
Regular Testing: Conduct regular tests to verify accuracy across different product types.
8. Data Management and Analysis
Challenge:
Many manufacturers struggle with managing and analyzing checkweighing data effectively. Poor data management can lead to inefficiencies and missed opportunities for process improvement.
Solution:
Implement Data Analytics Software: Utilize software that collects, organizes, and analyzes checkweighing data in real-time.
Set Up Automated Reports: Generate automated reports to track trends and identify areas for optimization.
Leverage AI and Machine Learning: Use AI-driven analytics to predict potential issues and enhance decision-making.
Conclusion
Industrial checkweighing is essential for maintaining product quality, optimizing production efficiency, and ensuring regulatory compliance. However, several challenges can hinder its effectiveness. By implementing best practices such as regular calibration, preventive maintenance, data analytics, and proper integration with other systems, manufacturers can overcome these obstacles and improve their checkweighing processes. Investing in advanced technology and continuous training will further enhance accuracy, reduce downtime, and maximize overall productivity.
Write a comment ...